Frozen food refers to the food where qualified food raw materials are properly processed, frozen at a temperature of-30℃, and stored and circulated at-18℃ or lower after packaging. Due to the use of low temperature cold chain storage in the whole process, frozen food has the characteristics of long shelf life, not easy to corrupt and easy to eat, but it also puts forward greater challenges and higher requirements for packaging materials.
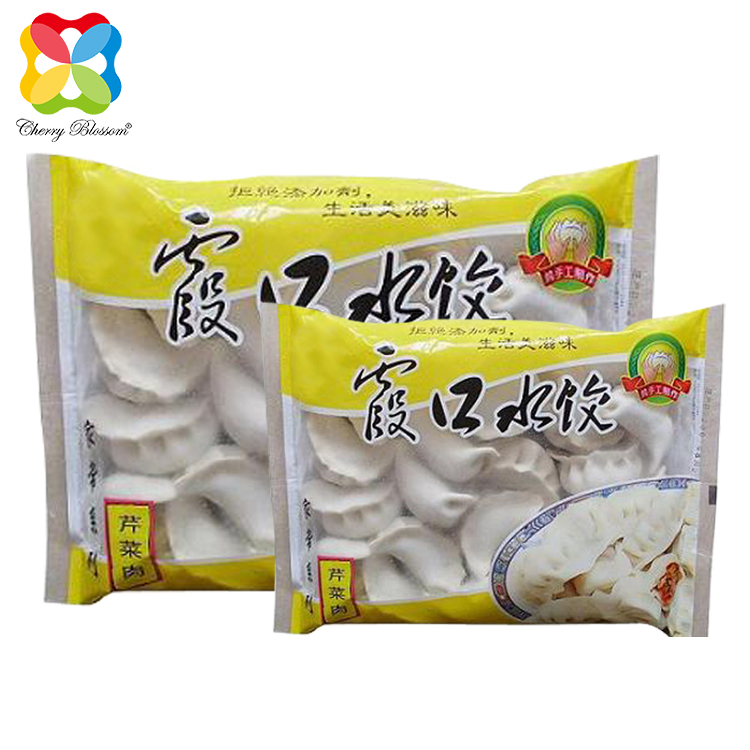
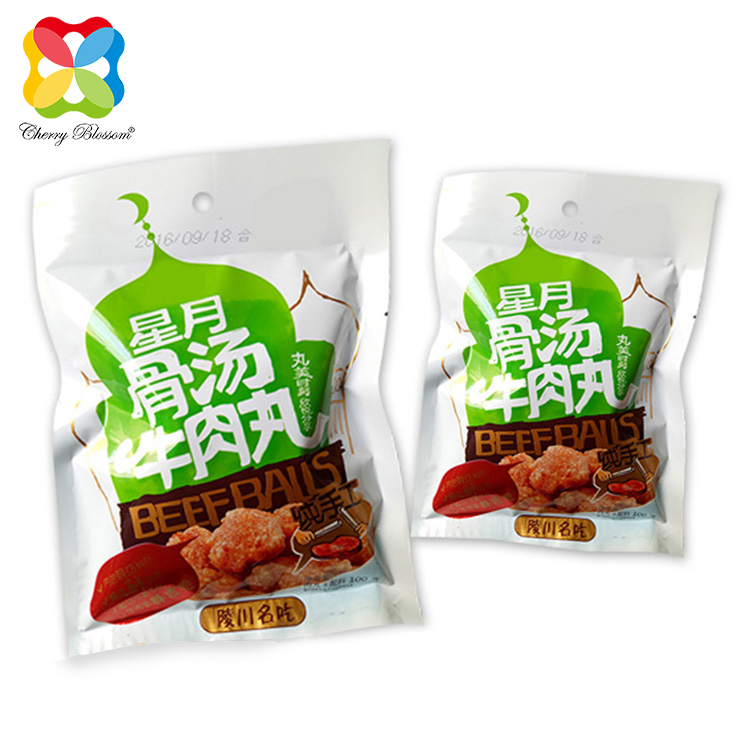
Common frozen food packaging materials
At present, the common frozen food packaging bags on the market mostly adopt the following material structure:
1.PET/PE
This structure is relatively common in the quick-frozen food packaging, moisture-proof, cold resistance, low temperature heat sealing performance is good, the cost is relatively low.
2. BOPP/PE, BOPP/CPP
This type of structure is moisture-proof, cold resistant, and has high tensile strength for low-temperature heat sealing, making it relatively cost-effective. Among them, BOPP/PE structure packaging bags have a better appearance and feel than PET/PE structure, which can improve the product grade.
3. PET/VMPET/CPE, BOPP/VMPET/CPE
Due to the presence of an aluminum coating, this type of structure has a beautifully printed surface, but its low-temperature heat sealing performance is slightly poor and its cost is relatively high, resulting in a relatively low usage rate.
4. NY/PE, PET/NY/LLDPE, PET/NY/AL/PE, NY/PE
The packaging of this type of structure is resistant to freezing and impact. Due to the presence of the NY layer, it has good puncture resistance, but the cost is relatively high. It is generally used for packaging products with edges or heavy weights.
In addition, there is another type of PE bag that is commonly used as an outer packaging bag for vegetables and packaged frozen foods.
In addition, there is a simple PE bag, generally used as vegetables, simple frozen food packaging bags, etc.
In addition to packaging bags, some frozen food needs to use plastic tray, the most commonly used tray material is PP, food-grade PP hygiene is good, can be used at-30℃ low temperature, there are PET and other materials. Corrugated carton as a general transportation packaging, its shock resistance, pressure resistance and cost advantages, is the first consideration of frozen food transportation packaging factors.
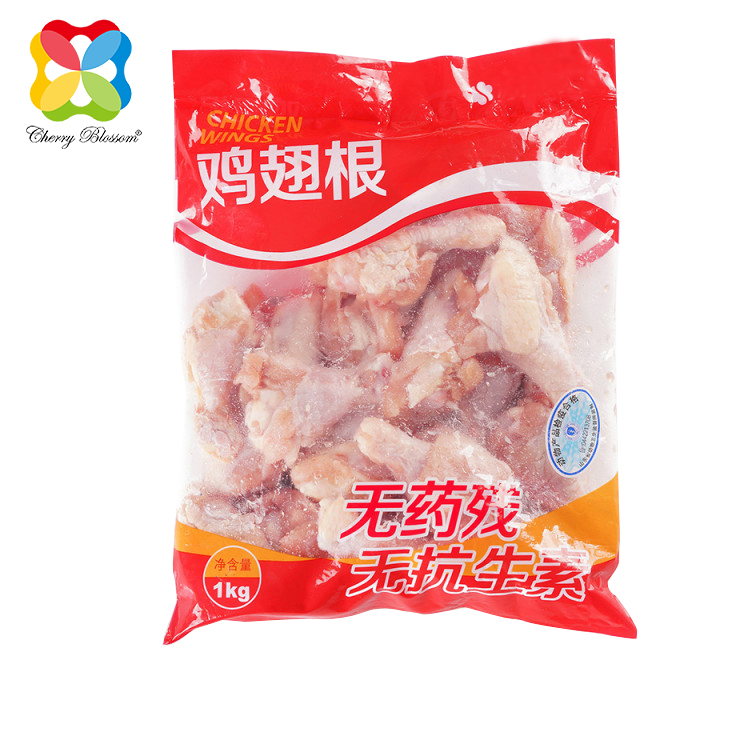
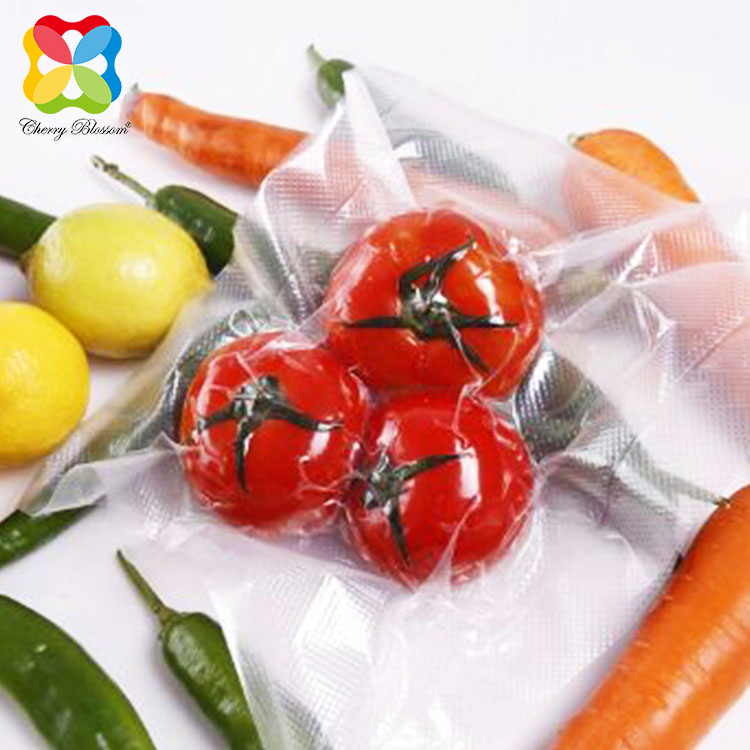
Two major problems cannot be ignored
1. food dry consumption, freezing burning phenomenon
Frozen storage can greatly limit the growth and reproduction of microorganisms, reducing the rate of food spoilage and spoilage. However, for certain frozen storage processes, the drying and oxidation phenomena of food will also become more severe with the extension of freezing time.
In the freezer, there is a distribution of temperature and water vapor partial pressure: food surface>surrounding air>cooler. On the one hand, this is because the heat on the surface of food is transferred to the surrounding air, further reducing its own temperature; On the other hand, the differential pressure of water vapor between the food surface and the surrounding air can promote the evaporation and sublimation of water and ice crystals on the food surface into the air.
At this point, the air containing more water vapor absorbs heat, reduces its density, and moves towards the air above the freezer; When flowing through the cooler, due to the extremely low temperature of the cooler, the saturated water pressure at that temperature is also very low. As the air is cooled, the water vapor contacts the surface of the cooler and condenses into frost, which increases the density of the cooled air and sinks and comes into contact with food again. This process will continue to repeat and circulate, and the water on the surface of the food will continue to be lost, resulting in a decrease in weight. This phenomenon is called "dry consumption".
During the continuous process of drying phenomenon, the surface of food will gradually become porous tissue, increasing the contact area with oxygen, accelerating the oxidation of food fats and pigments, causing browning on the surface and protein denaturation. This phenomenon is known as "frozen burning".
Due to the transfer of water vapor and the oxidation reaction of oxygen in the air, which are the fundamental reasons for the above phenomena, the plastic packaging materials used in the inner packaging of frozen food should have good water vapor and oxygen barrier properties as a barrier between frozen food and the outside world.
2. The Effect of Frozen Storage Environment on the Mechanical Strength of Packaging Materials
As is well known, plastics become brittle and prone to cracking when exposed to low temperatures for a long time, resulting in a sharp decline in physical properties. This reflects the weakness of plastic materials in poor cold resistance. Usually, the cold resistance of plastics is represented by the embrittlement temperature. As the temperature decreases, plastics become brittle and prone to fracture due to the decrease in the activity of their polymer molecular chains. Under the specified impact strength, 50% of plastics undergo brittle failure, and this temperature is the brittle temperature, which is the lower limit of the temperature at which plastic materials can be used normally. If the packaging materials used for frozen food have poor cold resistance, the sharp protrusions of frozen food can easily puncture the packaging during later transportation and loading and unloading, causing leakage problems and accelerating food spoilage.
Solutions
To minimize the frequency of the two major issues mentioned above and ensure the safety of frozen food, the following aspects can be taken into consideration.
1. Choose high barrier and high-strength inner packaging materials
There are a wide variety of packaging materials with varying properties. Only by understanding the physical properties of various packaging materials can we choose reasonable materials based on the protection requirements of frozen food, so that they can maintain the flavor and quality of the food and reflect the value of the product.
At present, plastic flexible packaging used in the field of frozen food is mainly divided into three categories:
The first type is single-layer packaging bags, such as PE bags, which have relatively poor barrier effect and are commonly used for vegetable packaging, etc;
The second type is composite soft plastic packaging bags, which use adhesives to bond two or more layers of plastic film materials together, such as OPP/LLDPE, NY/LLDPE, etc., with relatively good moisture resistance, cold resistance, and puncture resistance;
The third type is multi-layer co extruded soft plastic packaging bags, which melt and extrude different functional raw materials such as PA, PE, PP, PET, EVOH, etc., and merge them in the main die. They are blown, expanded, and cooled together. This type of material does not use adhesives, and has the characteristics of pollution-free, high barrier, high strength, and resistance to high and low temperatures.
Data shows that in developed countries and regions, the use of the third type of packaging accounts for about 40% of the total frozen food packaging, while in China it only accounts for about 6%, which needs further promotion.
With the continuous progress of technology, new materials are also emerging one after another, and edible packaging film is one of the representatives. It uses biodegradable polysaccharides, proteins, or lipids as the substrate, and forms a protective film on the surface of frozen food by wrapping, soaking, coating, or spraying, using natural edible substances as raw materials and through intermolecular interactions to control water transfer and oxygen permeation. This film has obvious water resistance and strong gas permeability resistance. Most importantly, it can be consumed with frozen food without any pollution and has broad application prospects.
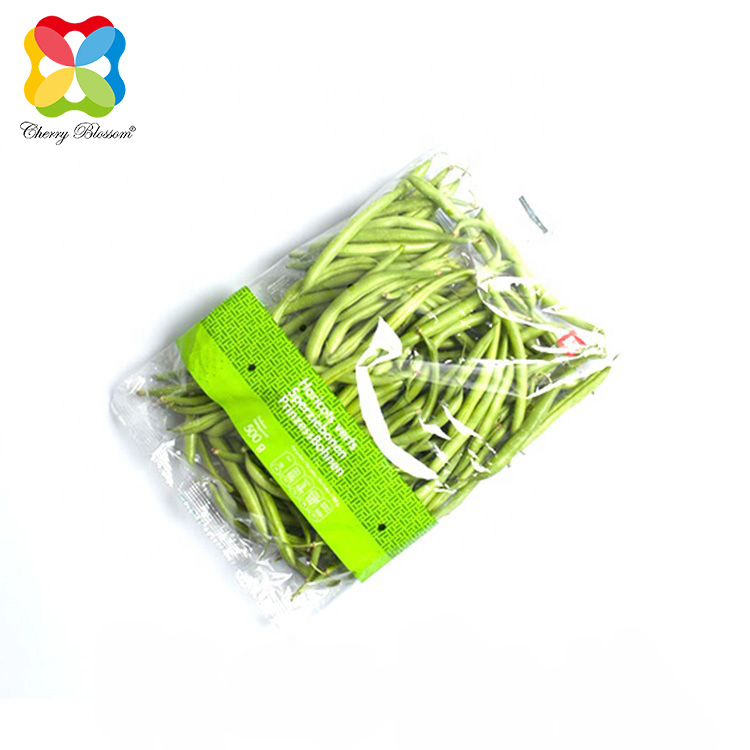
2. Improving the cold resistance and mechanical strength of inner packaging materials
Method 1: Choose reasonable composite or co extruded raw materials.
Nylon, LLDPE, and EVA all have excellent low temperature resistance, tear resistance, and impact resistance. Adding such raw materials in composite or co extrusion processes can effectively improve the waterproof, gas barrier, and mechanical strength of packaging materials.
Method 2: Increase the proportion of plasticizers appropriately.
Plasticizers are mainly used to weaken the secondary bonds between polymer molecules, thereby increasing the mobility of polymer molecular chains and reducing crystallinity. This is manifested by a decrease in the hardness, modulus, and brittleness temperature of the polymer, as well as an increase in elongation and flexibility.
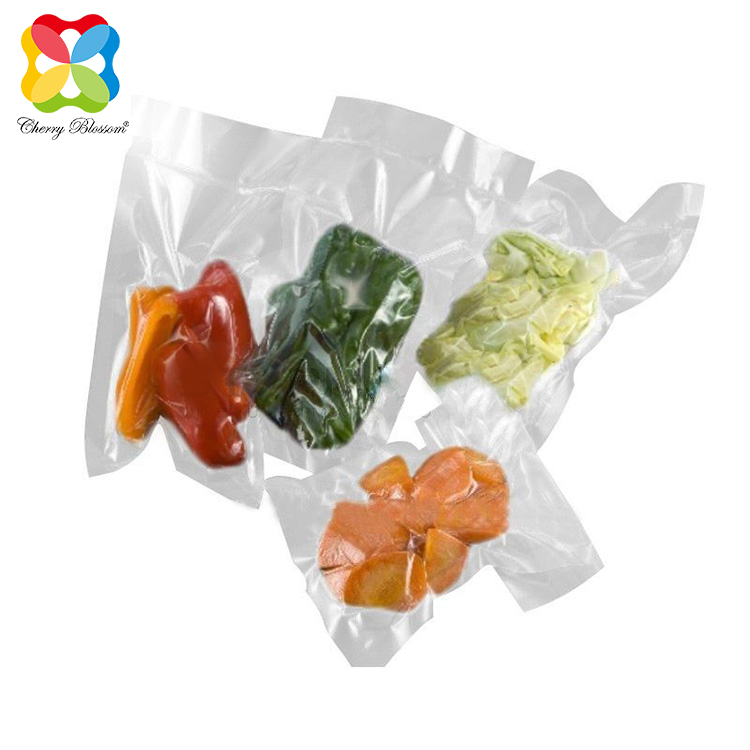
Strengthen packaging inspection efforts
Packaging is of great significance for frozen food. Therefore, the country has formulated relevant standards and regulations such as SN/T0715-1997 "Inspection Regulations for Transport Packaging of Frozen Food Products for Export". By setting minimum requirements for packaging material performance, the quality of the entire process from packaging raw material supply, packaging technology to packaging effect is guaranteed. In this regard, enterprises should establish a comprehensive packaging quality control laboratory, equipped with three chamber integrated block structure oxygen/water vapor permeability tester, intelligent electronic tensile testing machine, cardboard compression machine and other testing instruments, to conduct a series of testing tests on frozen packaging materials, including barrier performance, compressive performance, puncture resistance, tear resistance, and impact resistance.
In summary, packaging materials for frozen food face many new demands and problems in the application process. Studying and solving these problems is of great benefit to improving the storage and transportation quality of frozen food. In addition, improving the packaging inspection process and establishing a data system for testing various packaging materials will also provide a research foundation for future material selection and quality control.
If you have any frozen food packaging requirements, you can contact us. As a flexible packaging manufacturer for over 20 years, we will provide your right packaging solutions according to your product needs and budget.
Post time: Sep-27-2023