Flexible packaging composite pouches possess excellent barrier properties, heat-sealing properties, moisture resistance, as well as acid, alkali, and abrasion resistance. Hence, they are widely utilized in food outer packaging. With the increasing demands for the quality of flexible packaging composite pouches, packaging enterprises are attaching more and more importance to their quality inspection. This article will summarize the inspection methods of composite pouch products based on practice, hoping to be helpful to peers.
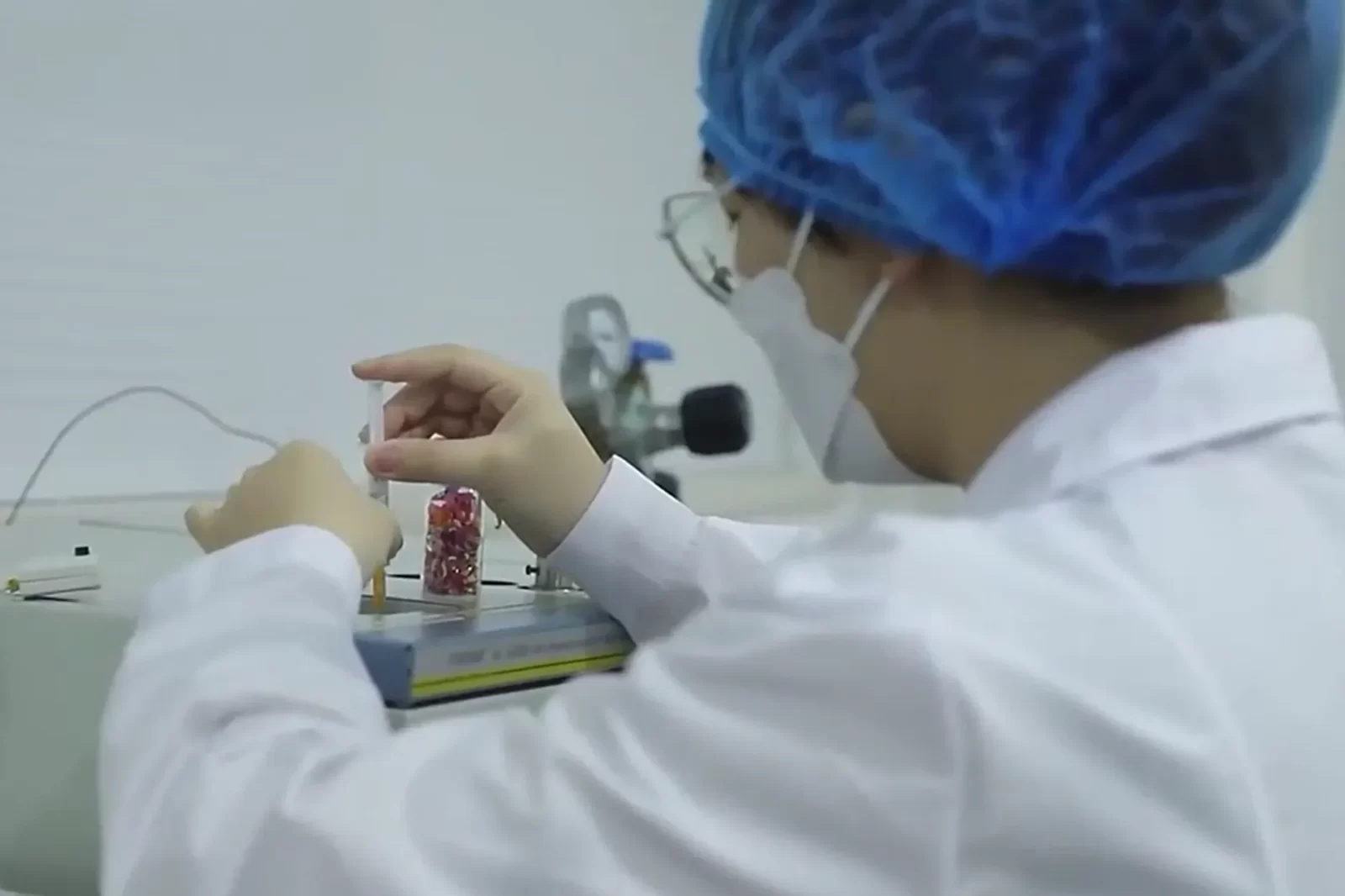
1. Visual Appearance Inspection
Visual appearance inspection encompasses the examination of the flatness and transparency of composite pouches and other items. It is mainly used to detect whether there are obvious scratches and pinholes on the surface of the composite pouch and whether there is contamination at the sealing part. Our company has a relatively complete set of appearance inspection methods, which are detailed as follows:
(1)Place the composite pouch in the palm of the hand and gently shake it in front of a 40W fluorescent lamp. Through the reflected light on the surface of the composite pouch, it is possible to clearly observe whether there are scratches or marks on the surface of the composite pouch. In the industry, this is often called "pouch surface scratching". If the scratching is severe, the root cause of the problem should be identified according to the actual situation to minimize the impact and ensure product quality. We have observed that most of the scratching phenomena are caused by the uncleanness of the drawing guide rollers of the bag-making machine.
Therefore, it is essential to ensure that the guide rollers are clean. In addition, if the guide rollers do not rotate, it will also cause scratching problems in the composite pouch. The reason for the guide rollers not rotating is mostly due to the lack of oil in the bearings. Therefore, good lubrication is the fundamental condition for the rotation of the bearings.
(2)Inspection method for the flatness of the composite pouch: Take several samples of finished pouches and drop them from a certain height onto the ground (the landing point should be clean), and observe the state of the composite pouch after landing. If the composite pouch bends, warps outward or arches inward when landing, it indicates that the flatness of the composite pouch is poor; conversely, it indicates good flatness.
The reasons for poor flatness are generally as follows: The bag-making temperature is too high, which has damaged the stress stiffness of the inner layer of the composite pouch; the structure composition is unreasonable; the material itself has uneven thickness. We have noticed that when the total thickness of the composite materials of pet/pe and bopp/pet/pe structures does not exceed 80μm, the phenomenon of poor flatness is more likely to occur.
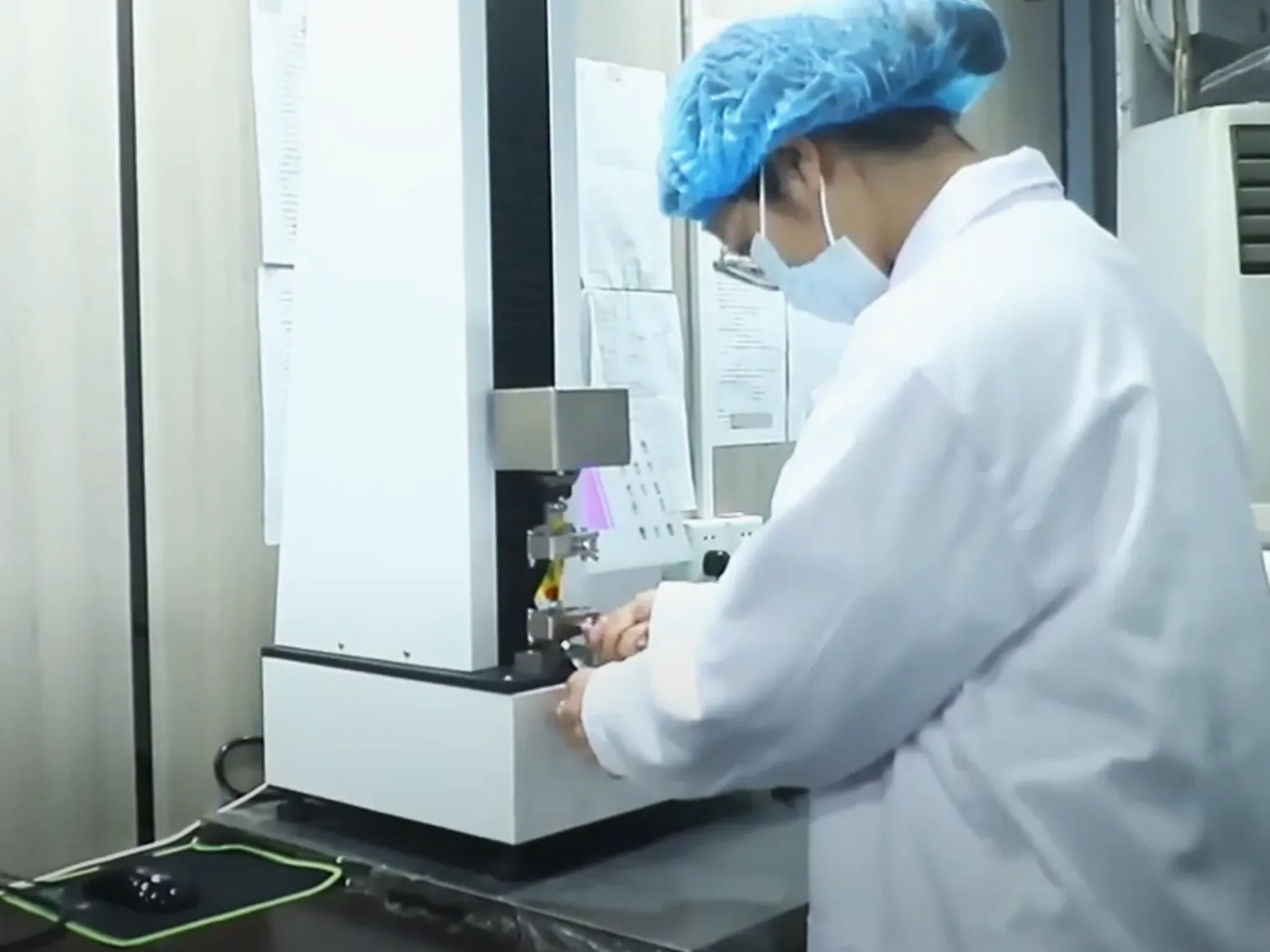
(3)Visual appearance inspection also includes the inspection of transparency. For some products with large areas without patterns, transparency is especially important. The detection method of transparency is as follows: Take a finished pouch and observe it through an indoor indirect light source. If there are "pockmarks", "rings", "foggy" and other phenomena in the blank area, it indicates poor transparency; otherwise, it indicates good transparency.
There are various reasons for poor transparency. For example, during the lamination process, if the color of the lamination adhesive itself is yellowish or reddish, the corresponding color shift will occur on the composite pouch, affecting its transparency. If the material itself has poor transparency and is "foggy", it will also affect its transparency. Therefore, strict quality control should be carried out when the materials enter the warehouse, and unqualified raw materials should not be allowed to enter. In addition, the transparency of different composite raw materials also varies. For example, the transparency of cast cpp is much higher than that of blown coextruded cpp.
2. Seal Integrity Inspection
Some tiny gaps at the sealing part may easily be overlooked during visual inspection, but they will lay a hidden danger for future food leakage. Therefore, it is necessary to conduct a seal integrity inspection on the composite pouch. The commonly used method is as follows: Spray a dye-added surfactant into the sealing part and observe whether it penetrates. If the color of the dye penetrates through the sealing part, it indicates that the sealing performance is poor; on the contrary, it indicates that the sealing quality meets the requirements. In practical work, we often use a small iron ruler with a length of 20 cm, a width of 5 cm, and a thickness of 0.8 mm, which is smooth and without burrs, to push and press the sealing part. If there are phenomena such as detachment and perforation when gently pushed, it indicates that the sealing performance is poor; if the sealing part still maintains the proper sealing dimension, it indicates that the sealing performance is good.
The reasons for poor sealing performance are as follows: The pressure of the sealing blade is insufficient or uneven. In this case, the problem can be solved by adjusting the spring pressure of the sealing blade; a low temperature will also cause poor sealing integrity at the sealing part of the composite pouch. We have noticed that when the total thickness of the composite materials exceeds 80μm, the problem of poor sealing integrity is more likely to occur during the bag-making process, especially for the bopp/opp structure. To ensure excellent product sealing integrity, there must be uniform and stable sealing pressure and an appropriate temperature.
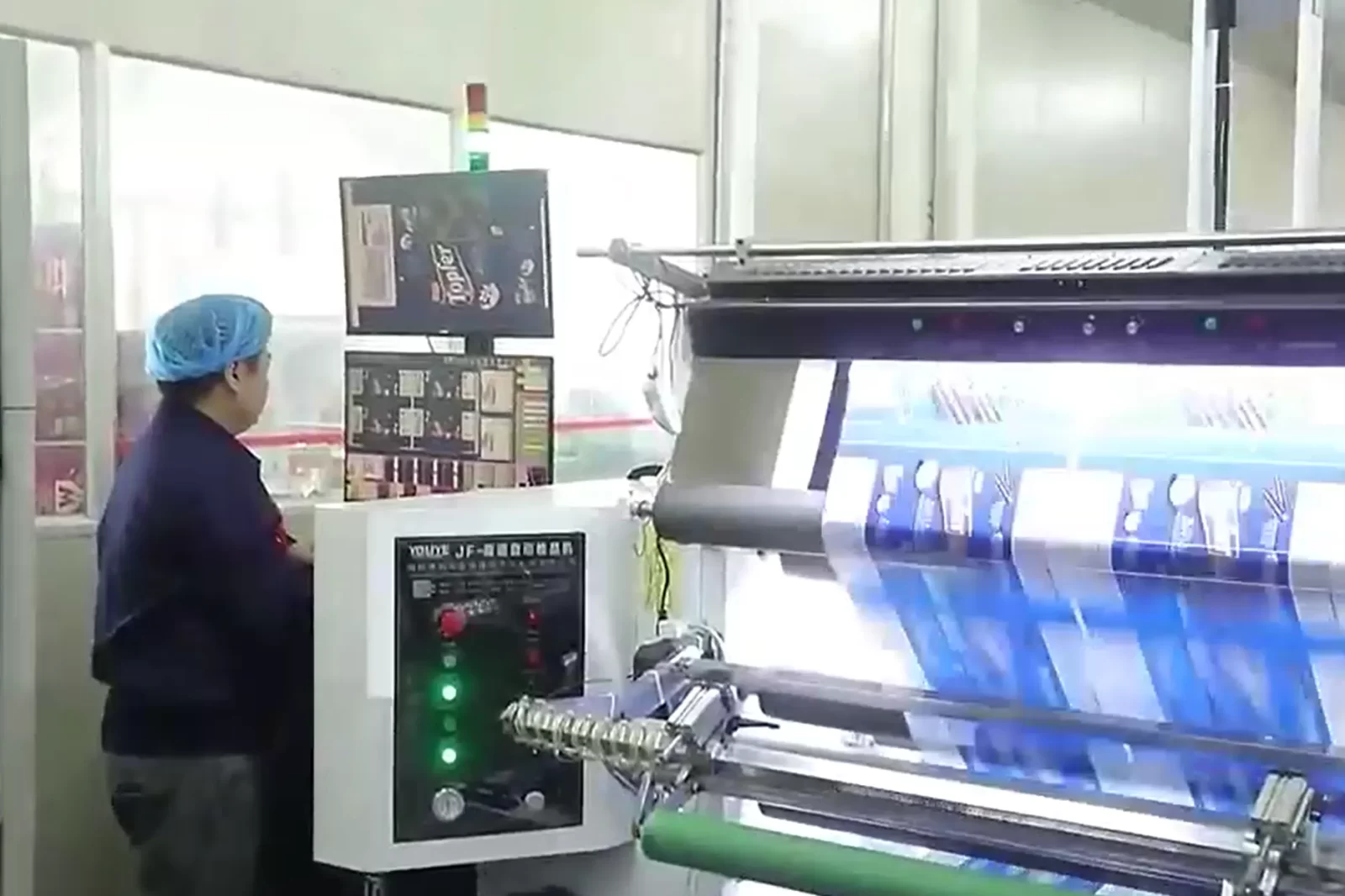
3. Seal Strength Inspection
In practical operation, another simple and feasible detection method is often used to detect the seal strength: Insert the index fingers of both hands into the opening of the composite pouch and tear it evenly in opposite directions. When the inner layer is cpe, the strength is much better than that of opp. When tearing, even if the sealing part is deformed, it will not cause delamination and detachment, which meets the seal strength requirements. If delamination and detachment occur when gently torn, it is regarded as an unqualified product with poor strength.
4. Leakage or Pinhole Detection
The dye penetration method is often used to detect the leakage or pinhole situation of vacuum composite pouches with extremely low air content. The specific operation is as follows: Add a colored surfactant into the pouch, seal it, place the pouch flat on the filter paper, and observe whether there is colored liquid on the filter paper after 5 minutes. Then turn the pouch over and test it again.
The water vacuum method can be used to test whether vacuum composite pouches with more air content leak. The method is as follows: Place the inflated and sealed composite pouch to be tested into a specific glass bottle filled with water, turn on the vacuum pump, reduce the pressure in the glass bottle to 1333 Pa (10 mmHg) within 30 - 60 seconds, and maintain it for 30 seconds. If bubbles overflow, it indicates that there is leakage.
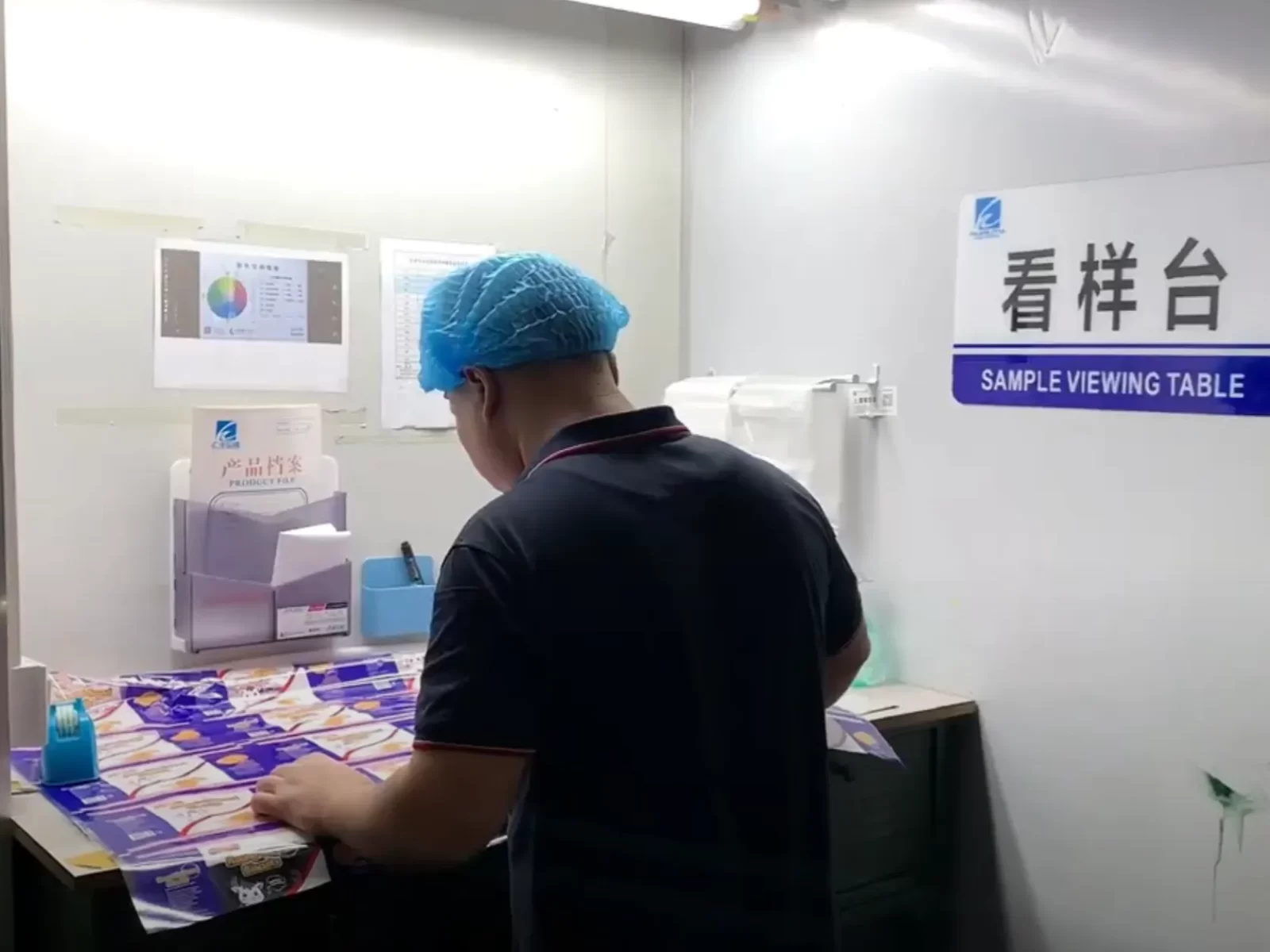
5. Compressive Strength and Burst Strength Inspection
The compressive strength inspection of composite pouches is also very important, aiming to test the bearing capacity of the composite pouches. The inspection method is as follows: Place the composite pouch horizontally on the platform, place a heavy object on it, keep it for 1 minute, and then take it down to check whether there is leakage at the sealing part. If there is, it is regarded as an unqualified product. The pressurization methods for flat-mouth composite pouches and box-shaped composite pouches are slightly different, and the pressurization time is 1 minute. The pressurization weight varies depending on the weight of the product itself.
The detection method of burst strength is as follows: Place the composite pouch to be tested between parallel plates with a gap of 1.27 cm, install a fixture and a rubber tube on the pouch, and slowly introduce compressed air into the pouch through this tube within 10 - 30 seconds until the internal pressure reaches the predetermined standard, and then maintain it for 30 minutes to observe whether it is damaged. Generally, the burst strength of commercial pouches should reach above 0.01 MPa.
6. Puncture Resistance Detection
Generally, the composite pouch drop test method is used. The specific operation is as follows: Drop the composite pouch products onto the rough cement floor once in the horizontal and vertical directions respectively. The drop height depends on the size and weight of the products in the composite pouch. When our company conducts this experiment, we often fill water into the pouch, seal it, measure it, and then conduct the drop experiment. In practice, the leakage situation is closely related to the thickness of the composite pouch and the quality of the composite pouch materials.
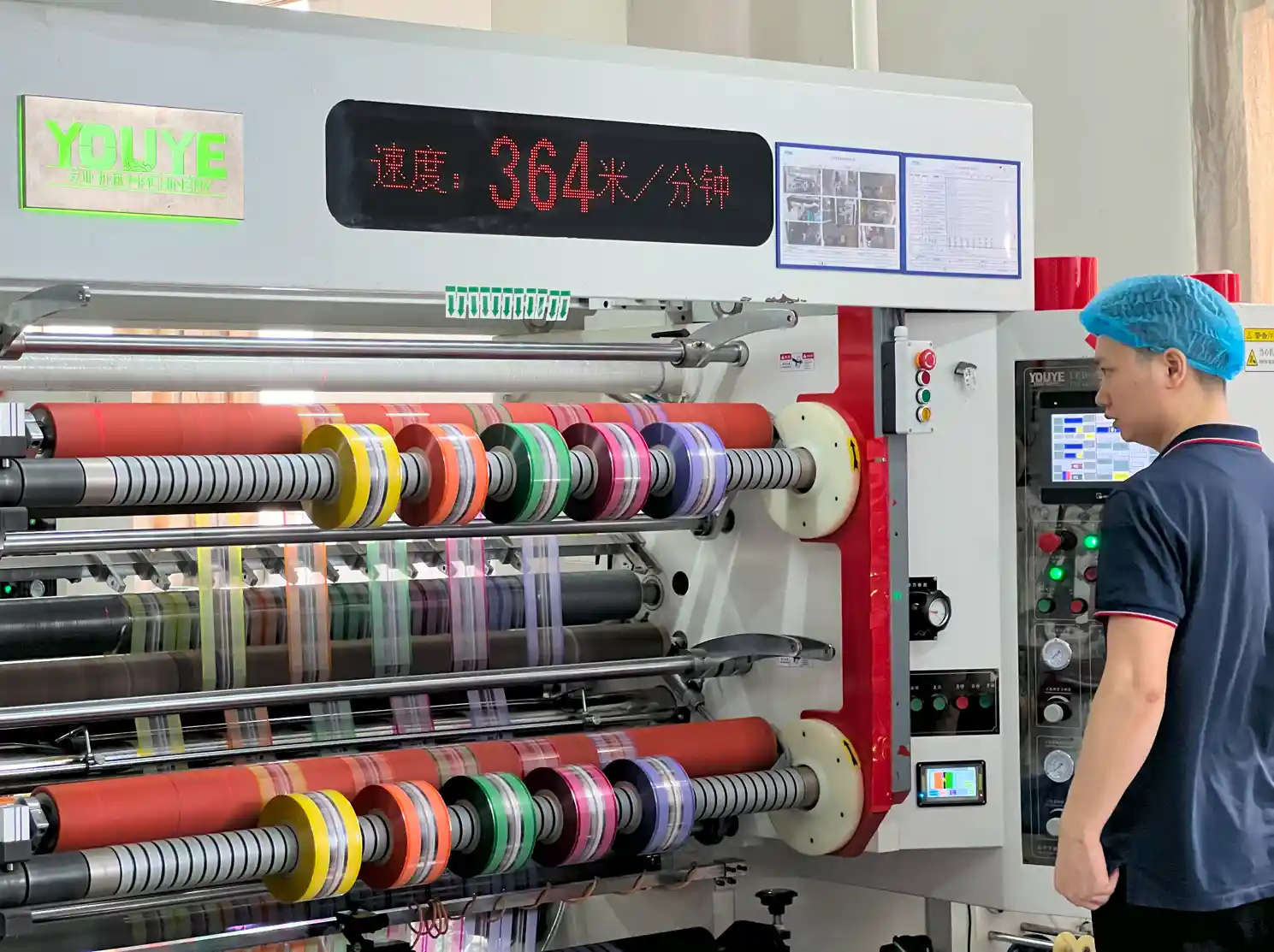
Post time: Jan-04-2025