With the continuous development of printing technology, the performance of equipment of many well-known printing brands has not only become better and better, but also the degree of automation has been continuously improved. The ink color remote control system has become the "standard configuration" of many intelligent printing, making the control of the ink color of printed products convenient and reliable. However, in the actual printing process, it is not easy to achieve stable ink color for each batch of printed products. Quality problems caused by large differences in ink color are often encountered in production, causing losses to the company.
Before printing, it is necessary to do a good job of pre adjustment based on experience
First, roughly adjust the ink volume of each color group ink fountain according to the area of the proof or printing plate. This work is easier to complete on a machine equipped with an ink remote control system. There should be an estimate of more than 80% for this. Do not adjust the ink volume in a large range while printing to avoid large color differences.
Secondly, according to the requirements of the production process sheet and the characteristics of the product, pre-adjust the feeder, paper collection, ink performance, pressure size and other links to avoid being in a hurry during formal printing. Among them, ensuring that the feeder can feed paper reliably, continuously and stably is the most important. Experienced operators first pre-adjust the blowing, suction, pressure foot, pressure spring, paper pressing wheel, side gauge, front gauge, etc. according to the format and thickness of the paper, straighten out the movement coordination relationship between the various components, ensure that the feeder feeds paper smoothly, and avoid different shades of ink due to the feeder hitting. It is recommended that experienced workers can pre-adjust the feeder.
In addition, the viscosity, fluidity, and dryness of the ink should be properly adjusted in advance according to the quality of the paper used and the size of the image and text area of the printed product to improve its printability and ensure normal printing. The ink color should not be uneven due to frequent shutdowns to clean the rubber cloth and the paper hair and ink skin on the printing plate. If various adhesive removers and ink oils are added in the middle of printing, color deviation is certain.
In short, doing a good job of pre-adjustment before starting the machine can greatly reduce the failure after the formal printing, and the captain will have time and energy to focus on the ink color.
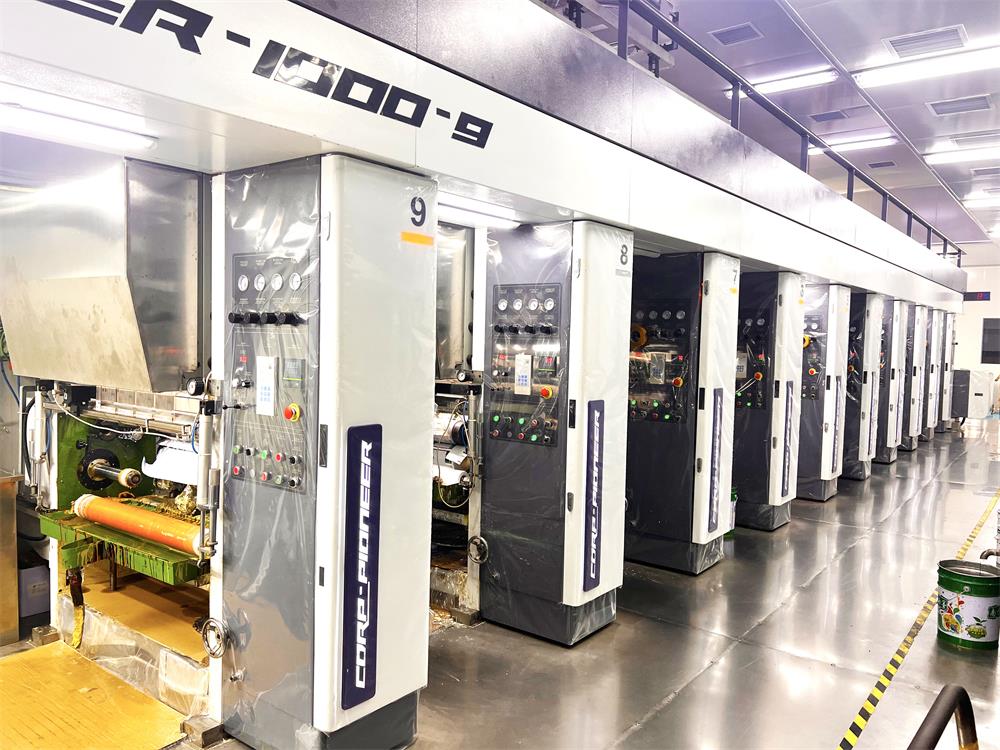
Correctly adjust the water and ink roller pressure
During the printing process, the image and text part of the printing plate must be continuously and evenly applied with an appropriate amount of ink to obtain a print with consistent ink color. Therefore, the ink rollers and the ink rollers, as well as the ink rollers and the printing plate, must maintain proper contact and rolling relationship to achieve good ink transfer. If this work is not done carefully and correctly, the ink color will not be consistent. Therefore, every time the water and ink rollers are installed, the method of rolling the ink bar is used to adjust the pressure between them one by one, instead of the traditional method of using a feeler gauge to test the tension, because the latter has a large actual error due to various human factors, and it should be banned on multi-color and high-speed machines. As for the width of the rolling ink bar, it is generally appropriate to be 4 to 5 mm. First adjust the pressure between the ink transfer roller and the ink stringing roller, then adjust the pressure between the ink roller and the ink stringing roller and the printing plate cylinder, and finally adjust the pressure between the water transfer roller, the plate water roller, the water stringing roller, and the intermediate roller, as well as the pressure between the plate water roller and the printing plate cylinder. The ink bar between these waterways should be 6 mm.
The equipment needs to be readjusted after two or three months of use, because the diameter of the ink roller will become smaller after a period of high-speed friction, especially in the transmission. The pressure between the ink rollers becomes smaller, and the ink will not be able to be transferred when the ink rollers accumulate on them. When the feeder pauses or stops to continue printing, the ink is large at this time, causing the ink color of the first dozens or even hundreds of sheets to be darker, and the ideal water-ink balance is difficult to achieve. This fault is generally not easy to find, and it is only more obvious when printing finer prints. In short, the operation in this regard should be meticulous and the method should be scientific, otherwise it will cause the water, ink bar, the mouth and tail of the print to have different depths of ink, artificially causing faults and increasing the difficulty of operation.
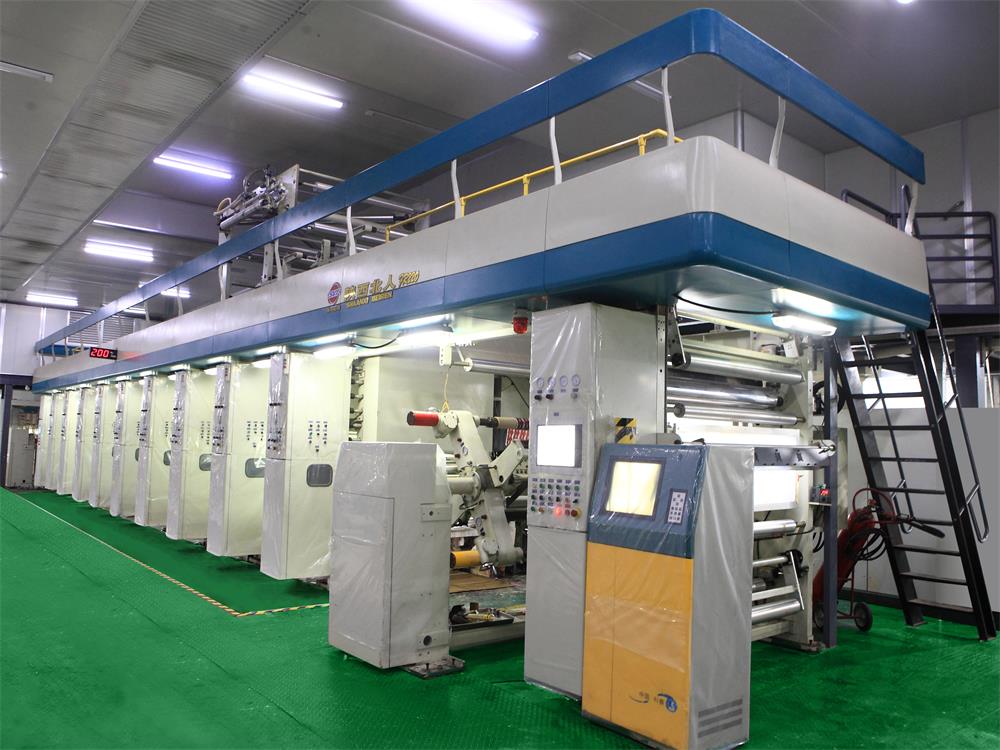
Achieving water-ink balance
As we all know, water-ink balance is an important part of offset printing. If the water is large and the ink is large, the ink will be emulsified in water-in-oil, and the quality of the printed product will certainly not be ideal. Through long-term practice, the author has explored some techniques.
First, ensure that the pressure relationship between the water and ink rollers is properly adjusted, and the content of the fountain solution and isopropyl alcohol meets the general standards. On this basis, turn on the machine, close the water and ink rollers, and then stop the machine to check the printing plate. It is best to have a slight 3mm of sticky dirt on the edge of the printing plate. Taking the amount of water at this time as the initial water amount for printing, the normal printing of general graphic products can be guaranteed, and the water-ink balance can be basically achieved.
Secondly, the amount of water can be flexibly adjusted according to other factors, such as the large area of the printing plate, the rough surface of the paper, the need to add additives to the ink, the printing speed and the changes in air temperature and humidity.
In addition, the author also found that when the machine is just started to print, the body temperature is low, and when the machine runs at high speed for one or two hours, the body temperature, especially the temperature of the rubber roller, will rise by more than double, or even higher. At this time, the amount of water should be gradually increased until the water-ink reaches a new balance.
It can be seen that it is not easy to achieve water-ink balance, and the operator needs to weigh and use it dialectically. Otherwise, the ink color stability is difficult to control, and high-quality printed products cannot be printed.
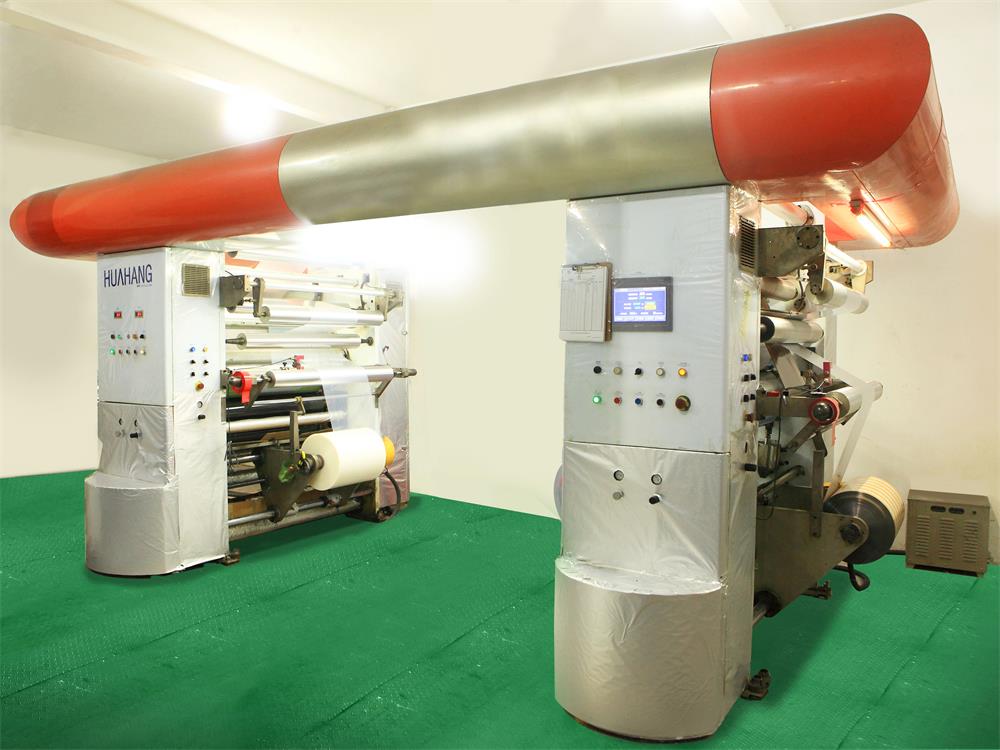
Proofreading and color sequence arrangement
In production, we often encounter such a situation: the sample provided by the customer is very non-standard, or only a color inkjet draft is provided without proofing. At this time, we need to analyze the specific situation, and we cannot use the method of rigidly increasing or reducing the ink volume to chase the effect of the proof. Even if it is close to the proof at the beginning, the stability of the ink color cannot be guaranteed, and thus the final quality of the printed product cannot be guaranteed. In this regard, the printing factory should actively communicate with the customer with a serious and responsible attitude, point out the problems and modification suggestions of the sample, and make appropriate adjustments before printing after obtaining consent.
In production, the printing color sequence of a multi-color machine is usually determined by the viscosity of the ink. Since in multi-color printing, the ink is superimposed in a wet-on-wet manner, only by obtaining the best superimposition rate can a stable and consistent ink color be printed. The arrangement of the printing color sequence must comply with the characteristics and quality requirements of the printed product, and cannot remain unchanged. At the same time, the viscosity of the ink can also be adjusted. For example, a purple cover and a sky blue cover have different printing color sequences: cyan first and magenta second for the former and magenta first and cyan second for the latter. Otherwise, the overprinted colors will be spotted, which is neither smooth nor stable. For example, for a print that is mainly black, black should be placed in the last color group as much as possible. This way, the glossiness of the black is better and scratches and color mixing inside the machine are avoided.
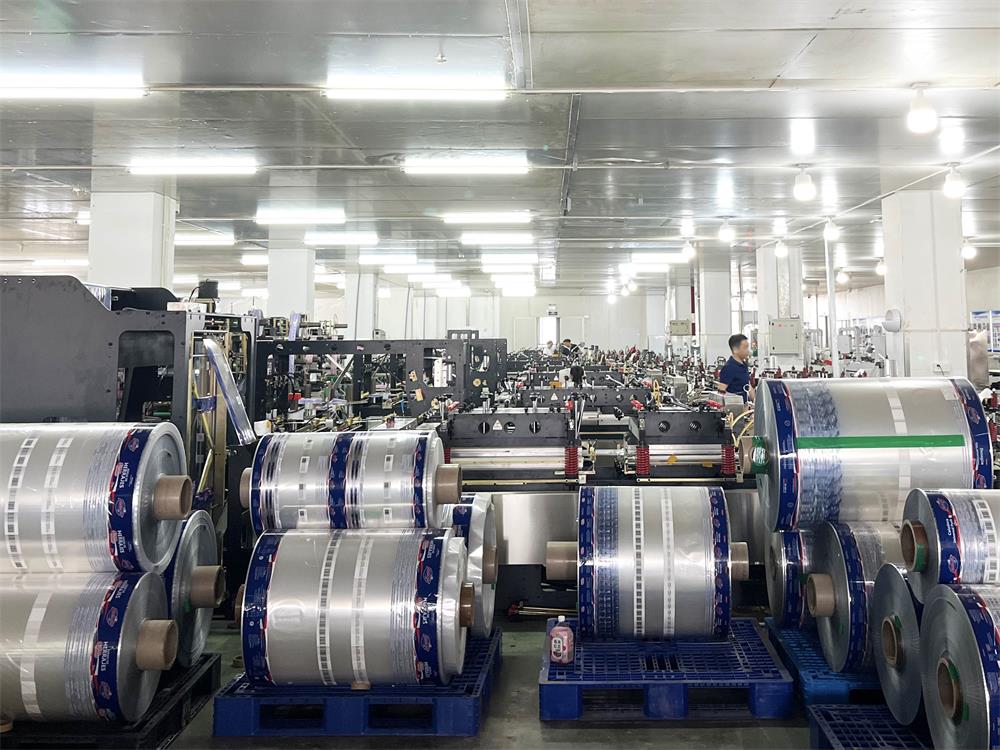
Cultivate good operating habits and strengthen work responsibility
When doing any work, we must have a high sense of responsibility and a strong sense of quality. We must standardize the process operation and adhere to good traditional habits such as "three levels" and "three diligences". Take the frequent comparison of samples as an example. When comparing the signature sample on the sample, due to differences in distance, angle, light source, etc., the visual will be biased, resulting in inconsistent ink color. At this time, the signature sample must be taken off the sample and compared carefully; the long-running printing plate needs to be baked to reduce the ink color deviation caused by plate change; the rubber cloth should be cleaned frequently, and more blotting paper should be placed after each cleaning to make the ink color stable; after the feeder is paused, the five or six sheets that have just been printed are too dark and need to be pulled out. The printing speed should not be too fast. The important thing is to keep the machine stable and normal; when adding ink to the ink fountain, because the new ink is harder and has poor fluidity, it should be stirred several times to avoid affecting the amount of ink and causing ink color deviation.
Operators should continue to learn, observe and analyze carefully, find out the factors that affect the change of ink color from all aspects, and take corresponding measures to properly prevent and overcome them, strive to improve the stability and consistency of the ink color of the printed products, and effectively improve the quality of the printed products.
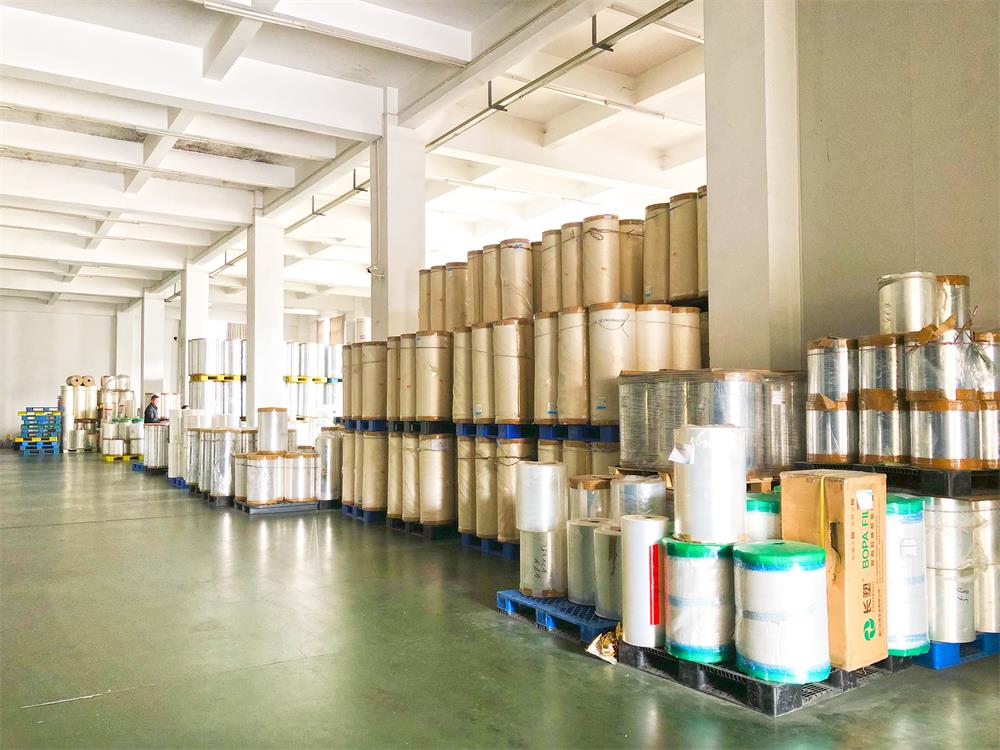
Post time: May-27-2024